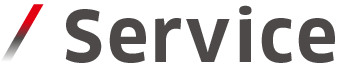
We offer design support during both basic and detailed design stage. We provide optimal solutions to
maximize the benefits of MAG Turbo while meeting your needs.
After delivery, we ensure the stable operation of the blower by providing necessary spare parts,
prompt support, periodic visits, and preventive maintenance by our experienced technicians.